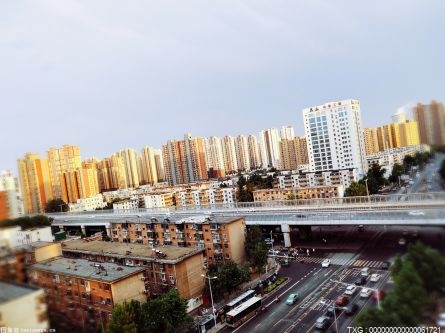
由于電池仍然是電驅(qū)動系統(tǒng)的最主要成本構(gòu)成,因此以最高效的方式使用電池提供的能量是很重要的,從電能到機械能的轉(zhuǎn)換效率即電驅(qū)動系統(tǒng)效率就顯得及其重要。為了提高效率,必須減少功率損耗:①逆變器的功率損耗必須保持在較低水平,②同時必須降低電動機的諧波損耗。碳化硅 (SiC) 技術(shù)的應(yīng)用,為 800 V 系統(tǒng)提供了實現(xiàn)這兩個目標(biāo)的可能性。 眾所周知,SiC功率器件比硅Si更高效,因為輕載導(dǎo)通損耗和開關(guān)損耗都更低。SiC技術(shù)可實現(xiàn)更高的開關(guān)頻率,從而通過降低諧波損耗來提高電機的效率。SiC半導(dǎo)體材料特性、效率優(yōu)化的模塊設(shè)計以及改進的控制技術(shù)相結(jié)合,組成了由逆變器 和電機組成的高效牽引系統(tǒng)。對于優(yōu)化設(shè)計后的系統(tǒng),在 WLTP 循環(huán)中,驅(qū)動系統(tǒng)效率可提高4?8%。
(資料圖片僅供參考)
1. 電驅(qū)動系統(tǒng)效率提升
純電動汽車 (BEV) 的成功取決于兩個主要方面。汽車的購置成本和客戶可用性。BEV 的電池續(xù)航里程仍然是客戶可用性最重要的特征之一。電池續(xù)航里程定義了每次電池充電的最大行駛距離和長途旅行的充電時間。這兩個標(biāo)準(zhǔn)都會受到牽引系統(tǒng)電壓水平的影響。更高的 800 V 系統(tǒng)電壓而不是 400 V 的通用電壓允許在恒定電纜橫截面下更快地為電池充電(大功率充電、超快速充電)。 目前的產(chǎn)品中,IGBT用作逆變器中的開關(guān)元件,在 800 V 的電壓下表現(xiàn)出效率劣勢,因為IGBT開關(guān)損耗太大。要高效使用更高的電壓,需要更高效的開關(guān)技術(shù),請參見圖1. SiC?MOSFET的應(yīng)用,可以滿足在高電壓平臺下高開關(guān)頻率的高效優(yōu)勢,以及高壓擺率 (dv/dt) 。更高的開關(guān)頻率降低了電機的諧波損耗。因此,SiC是通往更高系統(tǒng)電壓的關(guān)鍵技術(shù)。 如果可以找到電機和逆變器的兩條隨開關(guān)頻率相反運行的損耗曲線之間的最佳平衡,則 WLTP 系統(tǒng)級(800 V Si 系統(tǒng)與 800 V SiC 系統(tǒng)相比)的效率可能提高 4 % 至 8 %)。效率描述了存儲在電池中的能量與用于產(chǎn)生牽引力的能量之比。 因此,更高的效率可以實現(xiàn)在電池容量相同的情況下更長的里程,或者在電池容量降低的情況下產(chǎn)生里程不變。因此,提高效率是優(yōu)化 BEV 成本的最大措施。SiC 技術(shù)應(yīng)用帶來的是系統(tǒng)成本優(yōu)勢,因為它們可以節(jié)省更多的電池。 Vitesco Technologies 正在開發(fā)一種模塊化逆變器概念,用于從 400 V 到 800 V 的過渡。該開發(fā)的技術(shù)平臺是基于高度集成的電驅(qū)動系統(tǒng)EMR4( 第 4 代)。EMR4 電驅(qū)動橋是 EMR3 的進一步發(fā)展,目前已在中國進行大規(guī)模批量生產(chǎn)。EMR3 已集成到歐洲和亞洲 OEM 的多款車輛中。 EMR4 的電力電子控制器(逆變 )基于第四代電力電子控制器平臺(EPF4.0)。Vitesco Technologies 可以利用其在逆變器技術(shù)開發(fā)方面的廣泛和長期經(jīng)驗來實現(xiàn)具有低雜散電感和優(yōu)化 dv/dt 的技術(shù)。具有 SiC MOSFET 的 800 V 牽引系統(tǒng)的高效電力電子控制器的開發(fā)將通過 EPF 4.0的擴展實現(xiàn)。
2. 開關(guān)頻率和電壓壓擺率(dv/dt)在系統(tǒng)層面的影響
在電機運行期間,逆變器將電池提供的直流電壓轉(zhuǎn)換為快速脈沖電壓。該脈沖電壓會產(chǎn)生諧波交流 (AC) 電流。交流相電流產(chǎn)生轉(zhuǎn)子跟隨的旋轉(zhuǎn)電磁場。通過這種方式,脈沖電信號逐漸接近均勻正弦波形(40 kHz 及更高)的最佳值,高頻損耗減小。電流的頻譜變得“更干凈”,從而減少了以發(fā)熱形式出現(xiàn)的諧波損耗。 圖2 顯示了損耗開關(guān)頻率之間的關(guān)系? 其中: 電機的總損耗 – PL,EM,total 逆變器總損耗 – PL,PE,total – 在牽引系統(tǒng)的某個工作點。 電機損耗曲線為綠色,紅色為電力電子損耗。 特性曲線描述了每個參數(shù)的開關(guān)頻率的理論相關(guān)性:隨著開關(guān)頻率的增加,電機諧波損耗Ph,total 逐漸減少,所以總電機損耗 PL,EM,total 逐步向純正弦電流波形產(chǎn)生的鐵損值收斂 PL,total (水平虛線)。顯示的圖表是電機高分辨率 FEM 模擬的結(jié)果 ?;疑珮?biāo)記頻率區(qū)域的頻率相關(guān)功率損耗的準(zhǔn)確性相對于20kHz之前要低,由于仿真的模擬步長為5us。 逆變器總損耗 PL,PE,total 由導(dǎo)通損耗PL,cond和開關(guān)損耗 PL,SW 組成,開關(guān)損耗隨開關(guān)頻率線性增加。同時,該半導(dǎo)體的導(dǎo)通損耗不受開關(guān)頻率的影響。因此,逆變器總損耗預(yù)計會隨著開關(guān)頻率的增加而線性增加,與開關(guān)損耗的增加相同,見圖2。 上述分析基礎(chǔ)是一個 800 V 系統(tǒng),逆變器中使用了 SiC MOSFET。特征曲線在圖2 展示了 SiC 技術(shù)在逆變 功率模塊中的關(guān)鍵作用,作為實現(xiàn)最高系統(tǒng)效率的關(guān)鍵因素。圖2 進一步表明,系統(tǒng)級的最佳開關(guān)頻率必須定義為提高效率(平衡點)的影響因素。 與Si逆變相比,SiC逆變技術(shù)的全部潛力基于開關(guān)頻率和壓擺率高10倍的可能性。圖3演示了電壓壓擺率 (dv/dt) 對逆變損耗的影響。 帶有 SiC MOSFET 的高效 800 V 牽引系統(tǒng)的當(dāng)前開發(fā)研究了如何在不產(chǎn)生額外的干擾的情況下使用 SiC 技術(shù)的潛力(參見第 3 章和第 4 章),為了充分發(fā)揮 SiC 技術(shù)的潛力,必須考慮系統(tǒng)在高開關(guān)頻率和高電壓壓擺率下的電磁兼容性 (EMC) 以及噪聲振動 (NVH) 問題。如圖2所示,特別是較低的開關(guān)頻率對 NVH 具有關(guān)鍵影響。EMC正好相反,較高的開關(guān)頻率和壓擺率會導(dǎo)致更多的干擾。
3. 對逆變器的影響
當(dāng)今最先進的 400 V Si?IGBT 逆變 在 8 至 10 kHz 的開關(guān)頻率下運行。電壓壓擺率通常高達 5 kV/μs。圖 4 顯示了單個逆變系統(tǒng) (Si / SiC) 的差異以及不同輸出功率下產(chǎn)生的損耗。累積的總功率損耗分為開關(guān)損耗和導(dǎo)通損耗。 傳統(tǒng) Si 技術(shù)和 SiC 技術(shù)在 800 V 下的總功率損耗之間存在顯著差異。該圖證實了 800 V 電壓只能與 SiC 半導(dǎo)體一起使用。 評估逆變器的決定性因素是驅(qū)動系統(tǒng)在 WLTP 循環(huán)工況下的效率。圖 5 說明了逆變器對 WLTP 中系統(tǒng)效率的影響。條形圖的黃色部分顯示了 800 V SiC 相對于 800 V Si 解決方案的優(yōu)勢——盡管在這兩種情況下都只應(yīng)用了 10 kHz 的開關(guān)頻率和 5 kV/μs 的電壓壓擺率。配備 SiC 半導(dǎo)體的逆變 可能會在更高的頻率和轉(zhuǎn)換率下運行(典型值:開關(guān)頻率:10 ... 40 kHz,dv/dt:5 ... 50 kV/us)。左側(cè)的第二個欄圖 5 顯示了如果將 Si 逆變 用于800 V 系統(tǒng),損耗將如何變化。 圖1 - 5所示SiC技術(shù)在不同方面的更高效率是基于嵌入在硅中的碳原子在材料基體中的高載流子遷移率。 由于導(dǎo)通電阻低,在SiC半導(dǎo)體中產(chǎn)生的熱損失很低。這允許更高的開關(guān)頻率,緊湊的封裝空間和減少功率模塊的冷卻能力需求。因此,SiC半導(dǎo)體比Si半導(dǎo)體需要更小的封裝空間,可以實現(xiàn)更高的功率密度。 3.1 更高導(dǎo)電性的優(yōu)勢在今天的汽車牽引逆變器(400 V系統(tǒng)電壓水平和高達10 kHz的開關(guān)頻率)低損耗硅IGBT與一個并聯(lián)的二極管(自由運行分別回流到電池)。反向電壓(反電勢)在650…750之間時,IGBT需要比較復(fù)雜的控制,但由于在額定電壓下的高效率,它就像“完美的開關(guān)”一樣工作。Mosfet(金屬氧化物半導(dǎo)體場效應(yīng)晶體管:簡單地說:電壓控制電阻)更容易控制。在Si基半導(dǎo)體材料基礎(chǔ)上,在開關(guān)過程中Mosfet比硅IGBT有更高的電阻(R)(R在漏/源上= Rdson)。 在400 V時,較高的硅MOSFET功率損耗已經(jīng)不適用,在800 V時,它們被排除在選項之外(見圖5)。硅MOSFET的反向耐壓越高,其Rdson越高。在600v電壓水平以上,這種特點對整體效率有巨大影響。此外,還必須考慮在更高電壓下增加的冷卻成本。 在4H襯底(極高載流子遷移率的四元矩陣)中使用SiC技術(shù)的Mosfet在開關(guān)過程中表現(xiàn)出比使用Si技術(shù)更高的效率。低Rdson的優(yōu)勢是SiC MOSFET半導(dǎo)體在800 V逆變器應(yīng)用的主要原因。 較寬的帶隙和較低的表面電阻上較高的擊穿電壓,允許以較高的壓擺率切換高電壓,以上這些都是SiC的材料優(yōu)勢。由于更低的Rdson,開關(guān)損耗較低,可以應(yīng)用較高的開關(guān)頻率,見圖6。特別是在輕載時,低導(dǎo)通損耗有對工況效率意義巨大。 考慮到所有的限制條件,例如功率模塊的連接接口,SiC技術(shù)可能實現(xiàn)功率模塊體積減少25…50%。SiC比Si具有更高的導(dǎo)熱系數(shù),這為熱損耗的更好傳導(dǎo)散熱提供了可能。同時,SiC半導(dǎo)體可以在更高的溫度下工作。以上這些這就提供了逆變器設(shè)計要求的高功率密度條件。 綜合分析表明,SiC可以提高逆變器的效率,降低開關(guān)損耗,減少封裝體積,減少冷卻能力,提高工作溫度,減少功率模塊的重量。 與400V Si逆變器相比,400V SiC逆變器可以設(shè)計得更加緊湊。800V SiC逆變器需要更大的體積,因為爬電距離和電氣間隙要求更大。 原則上,SiC技術(shù)的優(yōu)勢也可以與400V系統(tǒng)結(jié)合使用,但只有在逆變器中才能實現(xiàn)效率優(yōu)勢。額外的優(yōu)勢,如超高速充電需要更高的電壓。為了研究SiC的優(yōu)勢,在整車上對一個400V SiC逆變器樣機進行了測試。采用SiC技術(shù)的800V逆變器目前正處于測試階段。 3.2 SiC的壓擺率(dv/dt)優(yōu)勢如圖7所示,在SiC半導(dǎo)體中,通過增加壓擺率dv/dt可以降低開關(guān)損耗。與硅相比,該技術(shù)具有更大的潛力,因為換相電路中較高的轉(zhuǎn)頻率和可調(diào)整的雜散電感降低了功率損耗。這就需要優(yōu)化柵極源電路中的雜散電感。由于換相電路中極低的雜散電感的實現(xiàn)成本相對較高,因此在系統(tǒng)級上定義平衡的dv/dt是優(yōu)化的一部分。 在一定的dv/dt下模擬雜散電感。結(jié)合開關(guān)頻率的增加,可以模擬一個WLTP周期的總功率損耗。在5…20kv /μs壓擺率范圍內(nèi),雜散電感處于較低水平時,對WLTP損耗是明顯的。 3.3 電磁兼容性眾所周知,高頻開關(guān)過程會引起電磁干擾。為了在牽引逆變器中應(yīng)用碳化硅Mosfet,必須研究高開關(guān)頻率和壓擺率與高屏蔽和濾波效果之間的權(quán)衡。圖8顯示了開關(guān)頻率加倍(10 kHz到20 kHz)對典型測量中的干擾頻和干擾強度。在20kHz時,干擾強度增加約6dB。僅僅提高開關(guān)頻率并不能得到最優(yōu)解決方案。必須研究SiC的最優(yōu)控制參數(shù),這將使系統(tǒng)具有良好的電磁兼容性能條件下,在可能的開關(guān)頻率下可接受的開關(guān)損耗得到最佳的效率增加。
4. 電機設(shè)計
800V應(yīng)用的一體化高效電驅(qū)動的開發(fā)基礎(chǔ)是大規(guī)模系列生產(chǎn)的EMR4電機系統(tǒng)。EMR4將比EMR3有更大的可擴展性,更多可能的子組件組合(作為800V逆變器選項)。此外,互連設(shè)計將更加標(biāo)準(zhǔn)化,互連的可擴展性也將提高。特別是在低功耗應(yīng)用中,組裝空間將會減少。與EMR4設(shè)計相比,通過改變互連設(shè)計,800V電機的線圈數(shù)量增加了一倍。 4.1 采用碳化硅技術(shù)提高電機效率第3章的功率損耗分析表明,在相同的冷卻能力下,SiC mosfet能夠?qū)崿F(xiàn)更快、更頻繁的開關(guān)。較高的開關(guān)頻率可以提高電機的效率。開關(guān)頻率越高,諧波電流越小。因此,增加開關(guān)頻率可以降低逆變器提供的諧波輸入功率。 圖9在功率流圖中演示了前面一節(jié)中描述的方面。通常的功率流(灰色)從輸入功率,通過氣隙功率,到軸上的機械輸出功率。定子和后來的轉(zhuǎn)子的功率損失是通過散熱傳遞的。紅色表示的是完全轉(zhuǎn)化為熱量而不影響機械功率的諧波輸入功率。采用碳化硅技術(shù)可以降低800V電機的諧波損耗。圖9 4.2 800V電機的設(shè)計參數(shù)眾所周知,變頻供電的電機比由恒定頻率的正弦波供電的恒速運行的電機應(yīng)力更大。圖10顯示了快速開關(guān)逆變器對電機造成的額外影響。800 V SiC技術(shù)的應(yīng)用需要更仔細地觀察電機的絕緣系統(tǒng)和軸電流。 雖然逆變器提供的上升時間很短的高頻電壓脈沖為高效系統(tǒng)創(chuàng)造了基礎(chǔ),但這些脈沖增加了對電機的壓力。特別是在高輸出功率時,可以觀察到最高的壓擺率。 系統(tǒng)設(shè)計的目標(biāo)是在低諧波損耗和由于高開關(guān)頻率和壓擺率而增加的絕緣系統(tǒng)要求和電機的使用壽命之間找到適當(dāng)?shù)钠胶?。這兩個方面的最佳平衡對碳化硅牽引系統(tǒng)的設(shè)計具有重要意義。 電機的絕緣系統(tǒng)必須承受過沖電壓,這是由于800V的電壓水平與高開關(guān)頻率和dv/dt的結(jié)合而產(chǎn)生的。 這些系統(tǒng)的測試電壓也會增加。電機和逆變器輸出端子之間的電纜長度必須設(shè)計得盡可能短,以防止由于反射電壓波而產(chǎn)生額外的電壓過沖。 圖10中的反射系數(shù) r 和電機阻抗 Z 說明了這一方面的問題。通過選擇最佳 dv/dt 以及最佳上升時間,應(yīng)考慮臨界電纜長度與上升時間直接相關(guān)。由于這種關(guān)系,電壓上升時間不能按需要選擇得那么高。這意味著要開發(fā) EMR4 的 800 V平臺,必須研究絕緣系統(tǒng)的行為和使用壽命。 高電壓峰值會導(dǎo)致局部放電,因為峰值電壓(例如導(dǎo)體和疊片之間的電壓)可以達到在薄弱點破壞絕緣系統(tǒng)的水平(PDIV問題)。這會導(dǎo)致絕緣系統(tǒng)在短時間內(nèi)發(fā)生故障。產(chǎn)生的電流會對絕緣系統(tǒng)產(chǎn)生永久應(yīng)力。結(jié)果,系統(tǒng)升溫并老化。 了解電壓脈沖對使用壽命的影響很重要。相應(yīng)的局部放電測量結(jié)果用于絕緣系統(tǒng)的設(shè)計。 此外,調(diào)速電機中存在在逆變器運行下引起高頻軸承電流的問題。這些包括由電機軸末端電位差引起的循環(huán)電流(軸、軸承、定子、定子外殼、軸承、軸),以及電容性軸承電流(也稱為 dv/dt 電流)和放電由于共模軸承電壓 Ub 的時間變化而產(chǎn)生的放電(EDM) 電流。 當(dāng)軸承潤滑劑的潤滑膜容量局部擊穿時,EDM 電流在高振幅放電電流峰值時出現(xiàn)。在汽車領(lǐng)域,EDM 電流被認(rèn)為與實際應(yīng)用相關(guān)。共模軸承電壓 Ub 與共模電壓 U0 的比值——所謂的軸承電壓比 (BVR)——可用于對預(yù)期 EDM 電流的初步估計。在不同工作點的軸承電壓的高分辨率測量中,可以觀察到特征電壓峰值,表明相關(guān)的放電電流??梢愿鶕?jù)軸承的使用壽命確定關(guān)鍵工作點。在確定潛在工作點后,對這些工作點的高比例進行連續(xù)測試,并評估軸承的使用壽命。如圖10所示,軸承電壓Ub 通過電容分壓器連接到共模電壓 U0。它由寄生電容(繞組外殼 Cw,h,繞組轉(zhuǎn)子 Cw,r 轉(zhuǎn)子外殼 Cr,h)和軸承阻抗 Zb 組成。等效電路圖顯示了防止 EDM 電流的措施,例如使用軸接地、定子繞組頭的靜電屏蔽或使用控制方法將U0降至最低。
5. 系統(tǒng)分析
前面的章節(jié)展示了 SiC 技術(shù)在組件級別的影響和可能性。下一步是在成本和效率方面將優(yōu)勢整合到優(yōu)化的牽引系統(tǒng)中,同時還要考慮 NVH 和 EMC問題。 5.1 在 WLTP 工況上轉(zhuǎn)移單個特征點為了根據(jù)扭矩-速度特性圖中的測量值評估 WLTP 工況下的有效性,選擇 WLTP 中累積最大的點作為測試的測量點。圖 11 顯示了帶有 EMR4 系統(tǒng)的 D級車驅(qū)動系統(tǒng)直方圖值。定義了 35 個操作點,并在電機測試臺上以不同的開關(guān)頻率結(jié)合不同的壓擺率進行測量。 5.2 測試結(jié)果的討論對測量結(jié)果的評估揭示了兩個對 SiC 技術(shù)的進一步發(fā)展具有決定性意義的關(guān)鍵發(fā)現(xiàn)。對于基本測量,在逆變器中實施了高電壓和低壓擺率。在某些操作點,高壓擺率對應(yīng)于10 kV/μs,低至5 kV/μs。 圖12顯示了在中速范圍內(nèi)低扭矩的一個工作點上器件級別和系統(tǒng)級別的功率損耗差異。逆變器的功率損耗預(yù)計會隨著開關(guān)頻率的增加而增加,并且在測量精度內(nèi)無法檢測到 5kV/μs 和 10kV/μs 之間的差異。這是由于依賴于操作點的壓擺率,它在低負載下的影響很小。另一方面,電機的功率損耗隨著開關(guān)頻率的增加而降低,但也會對 10 kV/μs 的更高電壓轉(zhuǎn)換率做出反應(yīng)。這一優(yōu)勢補償了由于更高的開關(guān)頻率而導(dǎo)致的系統(tǒng)級更高的逆變器損耗??偟膩碚f,它提高了系統(tǒng)效率。 在圖13中可以觀察到 10 kV/μs 對更高電流的逆變器級別的優(yōu)勢,因為整體逆變器損耗隨著逆變器電流(分別是逆變器輸出功率)的增加而增加。與低速下測得的性能相比,電機性能可能沒有變化,但在高于 8 kHz 的更高開關(guān)頻率下,在系統(tǒng)級僅觀察到微小的改進。通過調(diào)整更高的壓擺率,圖 13 中觀察到的優(yōu)勢應(yīng)轉(zhuǎn)移到特性曲線中的所有操作點。 5.3 WLTP 節(jié)能評估測量值用于校準(zhǔn)逆變器和電動機的仿真模型,以識別 WLTP 循環(huán)中的整體效率,并模擬未來的其他工況循環(huán)。為了初步表明SiC技術(shù)的效率潛力,系統(tǒng)級的測量損耗已轉(zhuǎn)換為特性圖。已經(jīng)通過適當(dāng)?shù)牟逯捣椒ń⒘俗銐蚓_的網(wǎng)格,以表示驅(qū)動模擬中的整個循環(huán)。圖14顯示了作為示例的特征系統(tǒng)圖,電壓壓擺率為5kV/μs,開關(guān)頻率為12kHz。 圖15顯示了D級車輛在WLTP循環(huán)中的結(jié)果,限值介于5kV/μs(6和12 kHz)和 10kV/μs(6和12kHz)之間。WLTP中PWM頻率的增加導(dǎo)致電機效率的增加。此外,它證實了逆變器輸出電壓壓擺率的增加會導(dǎo)致逆變器中6kHz和12kHz的電氣損耗降低。 根據(jù)圖14和15,計算出的逆變器損耗減少值低于開發(fā)目標(biāo)。因此,測得的工作點效率提高和隨后映射到 WLTP 表明,通過減少碳化硅半導(dǎo)體的開關(guān)損耗,WLTP 可以實現(xiàn)顯著優(yōu)勢。優(yōu)化的下一步是增加頻率和電壓壓擺率。 5.4 優(yōu)化從所進行的研究可以推斷,通過在逆變器中使用碳化硅半導(dǎo)體,除了調(diào)制方法和開關(guān)頻率變化等控制策略的經(jīng)典參數(shù)外,還可以使用新參數(shù)來提高效率。電壓壓擺率提供了除開關(guān)頻率之外優(yōu)化系統(tǒng)效率的可能性。Vitesco Technologies 擁有 iMCO 工具,能夠在多標(biāo)準(zhǔn)優(yōu)化中找到相關(guān)參數(shù)之間的最佳平衡。根據(jù)結(jié)果,可以開發(fā)控制策略,在潛在的批量生產(chǎn)中充分利用牽引系統(tǒng)中碳化硅半導(dǎo)體的潛力。
6. 總結(jié)與展望
由于提高效率的巨大力,半導(dǎo)體材料碳化硅的使用面臨著高壓應(yīng)用的突破。系統(tǒng)優(yōu)化提供了實現(xiàn)逆變器和電機最大效率的解決方案。使用 D 級車的例子,通部分工作點的效率提升分析,映射到它們對 WLTP 有效性的影響,提升WLTP工況里程。 眾所周知,碳化硅在開關(guān)狀態(tài)下比采用硅 IGBT 的當(dāng)前標(biāo)準(zhǔn)解決方案具有更高的電導(dǎo)率。在車輛層面,與 Si IGBT 相比,使用 SiC MOSFET 可將 800 V 電壓水平的系統(tǒng)效率提高多達 3%。除了這一優(yōu)勢之外,碳化硅還可以顯著提高逆變器輸出的電壓壓擺率 > 20 kV/μs(理論上),這是當(dāng)今的硅半導(dǎo)體解決方案所不能達到的指標(biāo)。與 Si IGBT 相比,在相同開關(guān)頻率下的逆變器可以進一步提高 2-4% 的效率。這已在某些操作點上得到驗證。然而,WLTP 中最佳開關(guān)頻率和電壓壓擺率的全部潛力的發(fā)揮需要進一步研究。 通過增加開關(guān)頻率,由于較低的諧波電流和較低動態(tài)損耗,電機得到了更高的效率。 開關(guān)頻率的增加通常會導(dǎo)致逆變器中開關(guān)損耗的增加。使用碳化硅半導(dǎo)體的解決方案可以通過提高電壓轉(zhuǎn)換率來降低作為逆變器開關(guān)頻率函數(shù)的整體開關(guān)損耗。這種效果可以積極地用于提高逆變器和電機系統(tǒng)的效率??傮w而言,電動機頻率的增加導(dǎo)致效率進一步提高 1-2%。為了減少效率劣勢,必須在 EMC 約束允許的情況下將電壓壓擺率調(diào)整為最高。通過使用 SiC 代替 Si 半導(dǎo)體,系統(tǒng)優(yōu)化在 800 V 的電壓水平下總共提高了 6 – 8% 的效率。 開關(guān)頻率增加到 20 kHz,電壓壓擺率增加到 15 kV/μs 是開發(fā)過程的下一步。這并不代表碳化硅可以獲得的最大可能值,但考慮到絕緣和 EMC 行為,這些參數(shù)在大規(guī)模批量生產(chǎn)中是可能的。 Vitesco Technologies 開發(fā)的逆變器在模塊化設(shè)計中進行了優(yōu)化,以使用碳化硅并實現(xiàn)最高效率。半導(dǎo)體和模塊設(shè)計的關(guān)鍵參數(shù)在系統(tǒng)范圍的優(yōu)化中被識別和調(diào)整。雜散電感的最佳范圍可以確定為優(yōu)化的關(guān)鍵參數(shù),以便在某個開關(guān)頻率下最小化開關(guān)損耗。 為了實現(xiàn) SiC 技術(shù)的效率提升,除了壓擺率和開關(guān)頻率的工作點相關(guān)調(diào)整之外,還必須軟件優(yōu)化及算法優(yōu)化進一步提升系統(tǒng)效率。
對于典型的 BEV,電池能量存儲通常在30到100kWh之間,這約小于等于335 英里的行駛里程。目前的快速充電技術(shù)額定功率為50kW,為電池充電需要35-120分鐘 ,但從消費者的角度來看,更快的充電時間可以最大限度地減少行駛里程限制帶來的不便。例如,通過將快速充電功率水平從50kW提高到150kW,充電時間減少了三分之二。但是,如果充電電壓水平保持在典型的400V,充電電纜的額定電流增加了3倍,體積變大,傳導(dǎo)損耗增加了9倍,需要改進冷卻系統(tǒng)以避免過熱。保時捷推出了800V系統(tǒng)電壓,充電速率高達350kW,這意味著只需 15 分鐘即可為 87kWh的電池充滿電。此外,ABB 還推出了模塊化“Terra Hp”充電系統(tǒng),能夠為400和800V電池充電,充電功率為175或350kW。
除了超快充電優(yōu)勢之外,與配備250-450V電池的傳統(tǒng)BEV 相比,800V BEV 還具備更多優(yōu)勢,包括在給定的電池電流限制下更快充電、由于較低的 I^2*R 損耗而導(dǎo)致的車輛損耗較低,以及由于電流較小而需要較小的電機和接線尺寸等。以前,為動力系統(tǒng)配備更高電壓水平的想法在豐田普銳斯中部分實施,僅用于電機和逆變器,其中在電池之后和逆變器之前采用升壓轉(zhuǎn)換器,以將直流母線電壓提高至650V用于提高電機性能并使其能夠在高速區(qū)域運行。此外,重型車輛是 800V 電池的主要應(yīng)用者,因為它們具有更高的運行功率,包括電動巴士和電動卡車。然而,更深入的研究對于評估動力總成電壓增加對不同動力總成部件的設(shè)計和性能的影響至關(guān)重要,本文填補了這一關(guān)鍵空白。
圖1顯示了 BEV 的基本配置,其中電池是動力總成組件的主要能源提供者。電池為兩個重要部分提供動力:通過逆變器作為動力總成核心的驅(qū)動電機和作為高壓(HV)動力總成和低壓(LV)動力總成中間部分的輔助電源(APU)配件和負載。目前,大多數(shù)BEV的電池電壓水平通常在250到450V之間變化。通過使用 800V電池,需要重新設(shè)計許多電氣組件以適應(yīng)新的電壓和電流。在本文中,進行了全面分析以研究使用800V電池對主要動力總成電氣組件的影響。第二部分討論了從400-V升級為800-V 對電池的影響。第III-VI節(jié)分別討論了400-V BEV中電機、逆變器、APU、充電機的現(xiàn)狀和技術(shù),以及使用 800-V 電池時對它們的設(shè)計和工作的影響。第七節(jié)總結(jié)了未來趨勢,第八節(jié)總結(jié)了本文。本系列先看到第四節(jié),下個系列我們繼續(xù)看后面的內(nèi)容。
1. 動力電池
車輛電池組由多個串聯(lián)和并聯(lián)的電池單元組成,因此可以針對任何電壓進行設(shè)計。迄今為止,大多數(shù)生產(chǎn)的BEV已將600V額定值的IGBT模塊用于其牽引逆變器,從而將其電池組電壓限制在400V左右的峰值。因此,BEV 通常使用約96個串聯(lián)連接的電池單元,例如,當(dāng)使用 4.2V 峰值鋰離子電池時,峰值母線電壓為 403V。迄今為止,此類電池組在車輛上運行良好,但充電功率受限于直流快速充電電纜的最大電流,這為使用 800-V 電池組提供了動力。
直流充電電纜可以提供的最大電流是因為需要電纜足夠輕便靈活,以便用戶輕松處理,將風(fēng)冷電纜限制在 250 A 左右,將液冷電纜限制在 500 A 左右,如表 I 所示。因此,400-V 電池組可以以大約 200 kW 的最大速率充電,如圖 2(a) 中電纜損耗與充電器電流和功率的關(guān)系圖所示。雖然 200 kW 是一個高功率水平,但在 20 分鐘或更短的時間內(nèi)為配備 100 kWh 大型電池組的車輛充電是不夠的,這是大多數(shù)下一代超快速充電車輛的目標(biāo)。將總線電壓增加到 800 V 允許使用相同的電纜將充電功率增加一倍,從而能夠以高達 400 kW 的極高速率充電。
為了說明400-V和800-V電池車輛之間的區(qū)別,可以對比具有400-V母線的特斯拉Model3和具有800-V母線的保時捷 Taycan。Model 3 和 Taycan 是兩種最快的充電車輛,分別在26 分鐘和22.5分鐘內(nèi)從5%的SOC充電到80%,它們采用了不同的設(shè)計理念。Model3的總線電壓較低,最大充電功率為 250 kW,這是通過使用 661 A 的非常高的最大充電電流來實現(xiàn)的,如表二所示。這種高充電電流對于 Model 3 來說可能是實用的,因為它采用了專有的充電系統(tǒng),該系統(tǒng)在每輛車的同一位置都有一個短電纜和一個插頭,最大限度地減少了插入車輛的人體工程學(xué)挑戰(zhàn)。保時捷 Taycan,在另一方面,憑借其 800-V 電池組,可實現(xiàn) 270 kW 的峰值充電功率,最大充電電流為 340 A,由傳統(tǒng)的直流快速充電器和插頭提供。兩種車輛的充電功率與電流的關(guān)系如圖 2(b) 所示,可以看到Taycan 的充電功率比 Model 3 略高,并且使用 800-V 可以實現(xiàn)高達 400 kW 的功率和 500 A 的充電電流。
雖然更高的電池組電壓對于增加最大充電功率是可取的,但它確實以額外的復(fù)雜性為代價。800V電池組需要兩倍數(shù)量的串聯(lián)電池,因此,需要兩倍數(shù)量的電池管理系統(tǒng) (BMS) 電壓檢測通道,電流傳感器、接觸器和溫度傳感器的數(shù)量可能不會改變。BMS 成本 CBMS 可以使用以下公式計算,其中 Ns 是串聯(lián)電池的數(shù)量,CVsense 是每個電池電壓感應(yīng)通道的成本,NTsense 和 CTsense 是溫度傳感器的數(shù)量和成本,CIsense、Ccontacto r、和 Ccontroller 分別是電流傳感器、接觸器和控制器的成本。通過常用組件的定價,可以確定 400-V 和 800-V 電池組的 BMS 成本之間的近似關(guān)系。假設(shè) 400-V 電池組使用 96 個串聯(lián)電池,800-V 電池組使用 192 個串聯(lián)電池,每個電池電壓感應(yīng)通道 2.25 美元,36 個溫度傳感器,每個溫度傳感器 1.00 美元,每個電流傳感器和接觸器 100 美元,和控制器的 50 美元,確定了400-V電池組的BMS總成本為602美元,800-V電池組的總 BMS 成本為818 美元。電流傳感器和接觸器成本基于 LEM CAB 500 汽車電流傳感器和 TE Connectivity EV200 接觸器的定價;考慮到外圍組件、印刷電路板、連接器和布線成本,假設(shè)電池電壓檢測成本是 AnalogDevices LTC6813 電池監(jiān)控芯片每通道成本的三倍;溫度傳感器和控制器成本是保守的假設(shè)。雖然任何電池組設(shè)計的成本結(jié)構(gòu)都是獨一無二的,但 800-V 電池組 BMS 的成本將不可避免地更高,如此處近似以及表 III 和 IV 所示(大約高出 1/3 或 200 美元的成本)。
800V 電池組需要 BMS 算法的額外計算復(fù)雜度,因為必須監(jiān)控更多的電池。800 V 電池組的電池組接觸器、保險絲和電纜的額定電壓也必須至少為 900 V,而 400 V 電池組的額定電壓則為 500 V。然而,對于 800V 電池組,在電池組和牽引逆變器、快速充電端口和其他 HV 系統(tǒng)之間傳輸電力的直流電纜的橫截面積可以減少,從而導(dǎo)致車輛質(zhì)量有所減少。例如,特斯拉 Model 3 在電池組和快速充電端口之間使用 3/0 AWG 銅纜。對于 800-V 系統(tǒng),將此電纜面積減少一半至一根 AWG 電纜,對于每米長的正極和負極電纜,可減少 0.76 kg 的銅質(zhì)量。任何電纜成本節(jié)約將取決于車輛中高壓電纜的總長度以及所用電纜之間的成本差異,并且可能轉(zhuǎn)化為 800V 車輛的數(shù)十美元成本節(jié)約。更高電壓的電池組還需要為 HV 組件提供額外的絕緣和間隙,如表 III 中所列,這可能會增加電池組的尺寸。
電池組電壓也會影響可靠性。具有四并聯(lián)五串聯(lián) (4p5s) 配置的示例電池組將在 25°C 下可靠地執(zhí)行約 1000 次循環(huán),而兩并聯(lián) 10 -series (2p10s) 配置包將可靠運行至僅 800 個周期。4p5s 配置代表 400-V 電池組,而 2p10s 配置代表 800-V 電池組,因為它的電池數(shù)量與 4p5s 配置相同,并且配置為兩倍電壓。高壓電池組的可靠性損失是由于單個電池故障對電池組容量的影響。更多的并聯(lián)電池,如在較低電壓組中出現(xiàn)的那樣,導(dǎo)致更高的可靠性,可靠性評價反映在表 IV 中分配的可靠性評級中。總之,從電池組的角度來看,主要800-V母線的動機是實現(xiàn)更高的充電率,最高 400 kW,最大充電電流為 500 A。對于不需要以如此高的速率充電的應(yīng)用,400-V母線可能仍會產(chǎn)生具有成本效益和能量密集的設(shè)計。為幫助車輛設(shè)計人員考慮權(quán)衡,表 IV 中提供了定性分析,其中強調(diào)了 400V 系統(tǒng)的BMS成本更低,能量密度和可靠性略高,因為 HV 匯流條周圍和印刷電路板上的電氣爬電距離和間隙要求降低。電路板,而 800-V 系統(tǒng)具有更小的電源線和更高的快速充電速率的潛力。表 III 顯示 400-V Model 3 和 800-V Taycan 電池組的能量密度分別為 163 和 148 Wh/kg,支持較低電壓電池組可以獲得更高能量密度的說法。切換到 800 V 電池組還有可能提高動力系統(tǒng)效率,特別是牽引逆變器效率,如第 IV 節(jié)所述。
驅(qū)動系統(tǒng)這種提高的效率可以允許電池組的一些尺寸縮小,并且這些成本節(jié)約以及直流電源布線的成本節(jié)約可以抵消 800-V 電池組的額外BMS成本。未來,隨著供應(yīng)商的組件變得越來越普及,以及工程師開始確定如何平衡車輛的成本效益和損失,越來越多的車輛可能會開始使用800-V母線架構(gòu)。
2. 驅(qū)動電機
近年來,牽引電機最重要的趨勢之一是向更高的直流母線電壓發(fā)展。相當(dāng)一部分商業(yè)化電機的直流母線電壓已超過500V。YASA 為 Regera 超級跑車開發(fā)的軸向磁通永磁 (PM) 電機可實現(xiàn)800V的直流母線電壓。保時捷 Taycan 是首批在生產(chǎn)中采用采用新型800-V技術(shù)的永磁同步電機的OEM 之一 。本節(jié)將討論為牽引電機應(yīng)用更高直流母線電壓的潛在優(yōu)勢和挑戰(zhàn)。
A. 電磁性能增強
作為一個突出的例子,Toyota Prius 驅(qū)動電機的最大直流母線電壓從2004年設(shè)計中的500V增加到2010年設(shè)計中的650V。升高的電壓范圍允許更高的速度運行,如圖 3 所示。假設(shè)穩(wěn)態(tài)運行并忽略定子電阻,永磁電機的相電壓:
其中 Ld 和 Lq 是 d - 和 q 軸視在電感,Id 和 Iq 是 d 軸和 q 軸電流,ω 是電角速度,m 是磁鏈。相電壓受逆變器最大輸出電壓 Vmax 的限制:
該電壓源自直流母線電壓,其中 ma 是調(diào)制指數(shù),Vdc是指直流母線電壓。因此,電機速度的約束可以計算為對于給定的設(shè)計,隨著直流母線電壓的增加,電機的基本速度成比例增加。
此外,較高的電壓允許較低的d軸電流以補償高轉(zhuǎn)速下的磁鏈并減少銅損。這反過來又確保了在弱磁區(qū)域更高的連續(xù)功率,并提高了電機功率密度。這就是為什么2010款普銳斯的電機功率密度比2004款車型提高了45%的原因。因此,從電磁性能的角度來看,將直流母線電壓增加到 800 V 將是有益的,因為由于擴展的速度區(qū)域,它降低了實現(xiàn)相同輸出功率所需的最大扭矩。由于電機尺寸通常與其扭矩能力成正比,電機體積和質(zhì)量也可受益于更高的電壓水平,從而帶來更高功率密度的牽引電機設(shè)計。
B. 熱和機械約束
考慮相同的額定功率,電壓越高,電流越小。這導(dǎo)致電纜橫截面積和質(zhì)量的減少。根據(jù)歐姆定律,較低的電流直觀地降低了銅損。另一方面,增加的電壓水平需要更多的串聯(lián)導(dǎo)體,這會導(dǎo)致相電阻的增加。正如 2004 年和 2010 年普銳斯電機效率曲線所證明的那樣,通過應(yīng)用更高的直流母線電壓可以實現(xiàn)更低的銅損和更高的效率。隨著轉(zhuǎn)速的增加,鐵損、機械損耗和交流銅損也會增加。這使得熱約束更加重要。由于更高的電壓導(dǎo)致的高速運行也帶來了機械應(yīng)力的挑戰(zhàn)。機械應(yīng)力與轉(zhuǎn)速的平方成正比 ,轉(zhuǎn)子應(yīng)設(shè)計良好并平衡,以減少偏心對電機性能的影響。可以采用一些技術(shù)來減少機械應(yīng)力,方法是添加加強筋或在轉(zhuǎn)子極片中引入凹槽 。但是,這些補救方法不可避免地會增加轉(zhuǎn)子結(jié)構(gòu)的復(fù)雜性。此外,電機的電磁性能受到改進的轉(zhuǎn)子結(jié)構(gòu)的影響,在所有這些方面,電機的多學(xué)科設(shè)計至關(guān)重要。
C. 局部放電風(fēng)險評估
電氣絕緣系統(tǒng)是電機正常運行的關(guān)鍵部件之一。高壓電機的一個重大挑戰(zhàn)來自定子絕緣系統(tǒng)中的局部放電 (PD)。PD(也稱為電暈放電)是當(dāng)電壓應(yīng)力超過臨界值時導(dǎo)體之間絕緣的瞬時擊穿 。伴隨著放電點附近絕緣層的侵蝕,這會導(dǎo)致絕緣系統(tǒng)的退化,并最終導(dǎo)致絕緣完全失效。因此,完全避免 PD 以確保電機的可靠性至關(guān)重要。
然而,當(dāng)直流母線電壓升高時,槽絕緣中發(fā)生局部放電的風(fēng)險更高。更嚴(yán)重的是,電力電子逆變器產(chǎn)生的脈寬調(diào)制 (PWM) 波形會在電機端子處產(chǎn)生復(fù)雜的過電壓,實際測量的最大過電壓高達直流鏈路電壓的兩倍。因此,當(dāng)使用 800V 直流母線電壓時,需要仔細評估絕緣系統(tǒng)中的 PD 風(fēng)險。
圖 4 描述了 PD 風(fēng)險評估的程序。為了確定最大過電壓,需要一個包含電壓源逆變器、傳輸電纜和電動機的系統(tǒng)模型。電壓尖峰隨幾個因素而變化,包括半導(dǎo)體器件的開關(guān)頻率、電纜長度、轉(zhuǎn)速和電機的扭矩水平。對于直流母線電壓為 800 V 的繞線電機,最大線間電壓可以超過 1 kV。
在計算出最大過電壓后,應(yīng)進行靜電分析估計定子槽內(nèi)的最大電壓應(yīng)力。考慮導(dǎo)體尺寸和絕緣厚度獲得電場分布。由于固體絕緣體的介電強度通常很高,因此在槽完全填充絕緣體的理想情況下,PD 不太可能發(fā)生。然而,絕緣體之間存在的小氣孔,無論是有意的還是由于可能的制造缺陷,都會顯著增加電壓應(yīng)力水平和 PD 風(fēng)險。氣體中的電壓應(yīng)力是固體絕緣體中應(yīng)力的幾倍,并且氣體的擊穿電壓應(yīng)力顯著降低 。根據(jù)Paschen定律評估具有小空隙的槽的PD風(fēng)險。如圖 4 的底部方塊所示,當(dāng)施加在空氣空隙上的電壓高于 Paschen 曲線上的擊穿電壓時,就會發(fā)生 PD,這也稱為 PD 起始電壓 (PDIV)。應(yīng)該指出的是,PDIV 與空隙厚度和壓力水平高度相關(guān)。此外,電機設(shè)計以及材料和包裝的選擇在降低局部放電風(fēng)險方面發(fā)揮著關(guān)鍵作用。因此,需要仔細設(shè)計電機以確保在較高的總線電壓下正常運行。
總之,在考慮電機電磁性能時,向 HV 移動是有利的,因為它可以提高電機功率密度,同時減輕電機重量。潛在的挑戰(zhàn)在于轉(zhuǎn)子結(jié)構(gòu)的穩(wěn)健性和 PD。使用目前的技術(shù),可以實現(xiàn)高達 20000 rpm 的運行速度,這對于 800-V 電機來說是令人滿意的??梢酝ㄟ^修改定子繞組配置或采用具有高介電強度的槽和線絕緣體來降低局部放電風(fēng)險。
從以上分析表明,從電機的角度來看,采用 800V 直流母線電壓是有利且可行的。
3. 逆變器
A. 400V BEV 中的逆變器
逆變器根據(jù)驅(qū)動器的需要調(diào)整電機的輸入電壓和電流以產(chǎn)生特定的扭矩和速度輸出。在 BEV 和 HEV 應(yīng)用中,電機和逆變器額定功率通常在 50 到 250 kW 之間。基于此功率范圍并根據(jù) BEV 應(yīng)用要求,例如高效率和高功率密度,眾所周知的架構(gòu)是兩電平半橋逆變器、三電平中性點鉗位 (NPC)圖 5 中顯示的逆變器和 Z 源逆變器。兩電平逆變器是目前主要拓撲結(jié)構(gòu),因為簡單和低組件數(shù)。兩電平逆變器由六個開關(guān)組成,每個開關(guān)的額定電壓等于電池電壓。逆變器性能的評估基于兩個主要標(biāo)準(zhǔn):輸出電壓的總諧波失真 (THD) 和輸入到輸出效率。
逆變器輸出電壓中較高的 THD 相當(dāng)于向電機繞組注入更多諧波,從而導(dǎo)致電機內(nèi)部出現(xiàn)更多功率損耗。因此,希望盡可能地降低 THD??梢愿鶕?jù)實施的調(diào)制技術(shù)和開關(guān)頻率來確定THD。正弦PWM(SPWM) 和空間矢量調(diào)制 (SVM) 是BEV 應(yīng)用中牽引逆變器的兩種常見控制技術(shù)。與SPWM相比,SVM在THD和效率方面顯示出優(yōu)勢,但其實現(xiàn)需要具有高計算能力的數(shù)字控制單元。為了提高效率和 THD,可以使用軟件和硬件方法。在軟件方法中,重點是增強調(diào)制技術(shù)的開關(guān)模式,以減少功率損耗或提高 THD。在硬件方法中,重點是利用寬帶隙 (WBG) 半導(dǎo)體,例如碳化硅 (SiC) 或氮化鎵(GaN) 開關(guān)。與硅MOSFET和IGBT相比,SiC 和 GaN 具有更快的開關(guān)行為以及更高的工作溫度額定值,從而導(dǎo)致更高的效率和更低的 THD。WBG 器件的更高工作溫度還可以降低逆變器熱管理系統(tǒng)的復(fù)雜性。
圖 5(b) 顯示了一個三電平 NPC 逆變器,與圖 5(a) 相比,它使用了更多的開關(guān),但每個開關(guān)的額定電壓是傳統(tǒng)兩電平逆變器的一半。與兩電平逆變器相比,三電平逆變器的最大優(yōu)勢是輸出電壓 THD 的顯著改善,從而減少了輸出端所需的濾波器尺寸。然而,平衡NPC逆變器的中性點電壓至關(guān)重要,這是一項具有挑戰(zhàn)性的任務(wù)。其它文獻中提出了多種控制技術(shù)來解決平衡問題,但與兩電平逆變器相比,控制要求更加復(fù)雜。此外,由于內(nèi)部開關(guān) [圖 5(b) 中的 Sa2 和 Sa3] 在一個電氣周期中與其他開關(guān)相比,功率損耗在三電平 NPC 中并不均勻。
圖 5(c) 提出的 Z 源逆變器。Z 源逆變器由一個兩電平逆變器組成,在輸入級有一個額外的 LC 網(wǎng)絡(luò),可以相應(yīng)地調(diào)整三個橋臂上的直流電壓。在 Z 源逆變器中,支路允許在每個開關(guān)間隔內(nèi)短時間短路。LC 網(wǎng)絡(luò)在短路間隔期間充電以在降壓或升壓模式下工作;與圖 5(a)和(b)所示的架構(gòu)相比,這是 Z 源逆變器的主要優(yōu)勢。以前的研究已經(jīng)研究了 Z 源逆變器在 BEV 和 HEV 應(yīng)用中的可行性。Z 源逆變器在燃料電池汽車中的使用較多,因為它可以降壓或升壓燃料電池電壓。此外,帶有簡單半橋降壓的傳統(tǒng)兩電平逆變器相比,Z 源逆變器采用更小的無源元件。然而,如果不需要降壓或升壓,傳統(tǒng)的兩電平逆變器是成本較低的選擇。
在本節(jié)中,選擇圖 5(a) 中所示的傳統(tǒng)兩電平逆變器用于比較 400-800-V 逆變器的案例研究,因為它是最常見的架構(gòu)。在第一個案例研究中,800-V 逆變器驅(qū)動 400-V 電機;第二,它以相同的輸出功率驅(qū)動一個 800-V 電機。第一項研究代表使用更高電壓的電池來改善快速充電的情況,但使用更傳統(tǒng)的 400-V 電機;第二項研究代表了整個車輛為 800-V 操作而重新設(shè)計的情況。對于這兩個案例研究,電機的額定功率相同,這意味著逆變器的額定額定功率也相同。
1) 第一個案例研究,800V逆變器驅(qū)動400-V 電機:對于 PMSM,轉(zhuǎn)矩與逆變器相電流成正比,而速度與逆變器相電壓的頻率成正比。因此,兩個假設(shè)逆變器的標(biāo)稱規(guī)格可以表示如下:
逆變器輸出功率可以表示如下:
其中 Vphase 是逆變器相電壓,? 是逆變器輸出電壓和一相電流之間的相位差。
以上等式可以組合得到以下:
圖5(a) 所示架構(gòu)的直流鏈路的標(biāo)稱電壓為 800 V,這意味著開關(guān)電壓額定值必須大于 800 V–1.2 kV。與可以使用 650V 開關(guān)的 400V 逆變器相比,這導(dǎo)致總成本更高。但是,800V 逆變器的標(biāo)稱開關(guān)電流將保持不變。輸入濾波電容器的額定電壓 [在圖 5(a) 中用 Cin 表示] 也增加到 800 V。Cin 所需的最小電容可以通過以下公式計算:
其中Iphase,rms表示逆變器相電流的 rms 值,Vdc% 是電容器上允許的最大電壓紋波百分比,Vdc 是電容器的標(biāo)稱平均電壓,fs是逆變器開關(guān)頻率。對于 800V 逆變器,Iphase,rms 基于上面分析不變。如果假設(shè) 400-V 和 800-V逆變器的電容器兩端允許相同的電壓紋波百分比,并且使用相同的開關(guān)頻率,則只有 (9) 分母中的 Vdc 在 800-V 逆變器中加倍。因此:
電容器成本和尺寸可以根據(jù)電容器存儲的能量進行估算,表示為 E = 1/2CV^2。對于所描述的兩種逆變器,電容器標(biāo)稱儲能之間的關(guān)系:
式中E越大,電容越貴,體積越大,整個逆變器體積越大,功率密度越低。等式表明,如果兩個動力系統(tǒng)使用相同的電機,逆變器的總尺寸將從400-V BEV 增加到 800-V BEV。
對于兩電平逆變器,逆變器相對于調(diào)制指數(shù)的最大線間電壓由下式表示:
其中 Vl-l 為線間電壓線電壓,m 是調(diào)制指數(shù),Vdc 是輸入直流母線電壓。等式:
基于上述等式,對于每個特定的轉(zhuǎn)矩/速度工作點,800-V逆變器的調(diào)制指數(shù)是400-V 逆變器的一半。圖 6 顯示了特定開關(guān)頻率下輸出電壓 THD 和調(diào)制指數(shù)之間的關(guān)系。根據(jù)圖 6,THD隨著調(diào)制指數(shù)的降低而惡化。因此,根據(jù)等式,當(dāng)使用 400V 電機時,與 800V 逆變器相比,400V 逆變器將提供更好的輸出電壓和更低的THD。
2) 第二個案例研究,800V逆變器驅(qū)動800V 電機:電機輸出功率表示為 Pout = τ ω,其中 τ 是轉(zhuǎn)矩,ω 是角速度。在 PMSM 電機中,扭矩和反電動勢 (EMF) 可以分別表示為:
其中K1 和 K2 是常數(shù)系數(shù),p 是極對數(shù),ψp 是轉(zhuǎn)子 PM 的總通量,Is 是定子電流或逆變器相電流。基于上式,更高的輸出扭矩需要更高的相電流。同樣,具有更高速度的電機會產(chǎn)生更大的 EMF,并且需要一個逆變器,該逆變器能夠以其輸出電壓產(chǎn)生能力來克服 EMF。因此,本研究考慮了 800 V 額定電機,其扭矩為 400V假設(shè)電機的一半,速度為 2 倍,以適應(yīng)800V逆變器。最終傳動比將加倍以提供車輪所需的扭矩。扭矩降低 - 速度增加方法的優(yōu)越好處是基于電機的定子電流的降低。定子電流的降低顯著降低了電機繞組的傳導(dǎo)損耗。對于第二個案例研究,當(dāng)運行800-V電機時,對于800-V逆變器,以上等式可以像表 V 中那樣重寫。可以根據(jù)上述等式和表 V 計算和比較兩個案例研究的功率損耗。對于 SPWM 調(diào)制技術(shù),傳導(dǎo)損耗可以表示為 :
其中 Isw 和 Idi 分別是開關(guān)及其反并聯(lián)二極管的平均電流,Vsw 和 Vdi 是電壓開關(guān)及其體二極管的壓降,RON 是開關(guān)導(dǎo)通時結(jié)的內(nèi)阻。最后,Isw,rms 和 Idi,rms 是開關(guān)和體二極管的均方根電流。對于 SPWM 調(diào)制,Isw、Idi、Isw,rms 和 Idi,rms 可以根據(jù)表 VI 計算。
在表六中,I p代表逆變器相電流的峰值幅度。開關(guān)損耗可寫為:
其中EON和 EOFF是導(dǎo)通和關(guān)斷瞬態(tài)期間的能量損耗。EON和 EOFF可表示為 :
其中 Vds(t)是關(guān)斷和導(dǎo)通瞬態(tài)間隔期間開關(guān)的漏源電壓,Ids(t) 分別是關(guān)斷和導(dǎo)通瞬態(tài)間隔期間的開關(guān)電流。在上述等式中,t0 是從關(guān)斷模式到導(dǎo)通模式的瞬變開始時間,tr是總上升時間。t1 是從開啟模式到關(guān)閉模式的瞬變開始時間,t f 是總下降時間。在等式中中,Vds(t0) = Vdc, Vds(t0 + tr ) =0,Vds(t1) = 0, Vds(t1 + tf) = Vdc, Ids(t0) = 0, and Ids (t1 + tf ) =0。然而,由于逆變器輸出電流是正弦的,Ids(t0 + tr ) 和 Ids(t1) 在電循環(huán)期間在上述等式中變化。因此,在一個電氣周期期間,EON 和EOFF 從一個開關(guān)周期變?yōu)榱硪粋€。結(jié)合上述計算,得到了正弦電流的總開關(guān)損耗。對于正弦電流:
其中Emax 為 EON+ EOFF,當(dāng) Ids(t) = I p 時,總開關(guān)損耗由上述等式表示。為了獲得更好的評估,400- 和 800-V 逆變器選擇了SCT3017ALHRC11 和 SCT3022KLGC11。SCT3017ALHRC11 是 650V N 溝道 SiC 功率MOSFET,SCT3022KLGC11 是 ROHM 半導(dǎo)體的 1.2kV N 溝道 SiC 功率 MOSFET。表 VII顯示了功率損耗計算的進一步規(guī)范。圖 7 顯示了三個不同逆變器的功率損耗,這些逆變器由表 VII 中的開關(guān)組成,在 fsw = 50 kHz 下運行,額定功率為25 kW。在圖 7 中,400-V 逆變器在 m = 1 和 Iphase = 66 A 時產(chǎn)生其標(biāo)稱功率。由于 800 V 直流電壓,第二個逆變器在 m = 0.5 時產(chǎn)生相同的 Iphase = 66 A,并且被稱為帶有 400 V 電機的 800 V逆變器,因為逆變器相電流與400-V 的情況。第三個逆變器設(shè)計為在較低的相電流 Iphase = 33 A 下運行,就像設(shè)計用于 800 V的電機的情況一樣。因此,第三種情況稱為 800-V 逆變器和 800-V 電機。根據(jù)圖 7,800-V 逆變器和 800-V 電機的組合功率損耗最低,而800-V 逆變器和 400-V 電機組合的功率損耗最高。
圖8 顯示了圖 7 中描述的三個逆變器在其標(biāo)稱額定值(fsw = 50 kHz,cosFi = 0.9 和 Pout = 25 kW)下的不同功率損耗分量。圖 8 顯示運行 400 V 電機的 800 V 逆變器具有最高的總傳導(dǎo)損耗、最高的開關(guān)損耗和最高的總功率損耗。對于圖 8 中驅(qū)動 400-V 電機的 800-V 逆變器,可以根據(jù)損耗計算公式中較小的 m 來證明最高的體二極管傳導(dǎo)損耗是合理的,而體二極管的平均電流和 rms 電流增加時m 減小。圖 8 還展示了運行 800V 電機的 800V 逆變器的最低傳導(dǎo)損耗,這是由于相電流減半。雖然帶有 800-V 電機的 800-V 逆變器的開關(guān)損耗略高于 400-V 逆變器,但傳導(dǎo)損耗占主導(dǎo)地位,因此帶有 800-V 電機的 800-V 逆變器效率最高。因此,該分析表明,隨著用于快速充電目的的 800-V 電池的出現(xiàn),不再使用以前的 400-V 電機效率更高。
圖 9 比較了所考慮的三個逆變器的輸入電容器要求。根據(jù)圖 9(a),驅(qū)動 800V 電機的 800V 逆變器需要最少的電容來執(zhí)行相同的濾波效果。圖 9(b) 顯示運行 800V 電機的 800V 逆變器的總標(biāo)稱能量與傳統(tǒng)的 400V 逆變器相似,可以解釋為輸入電容器的總尺寸和成本為上述兩種情況大致相同??梢愿鶕?jù)圖 6 和表 V 比較三種逆變器的相電壓 THD,可以得出結(jié)論,400-V 逆變器和 800-V 逆變器與 800-V 電機具有相同的 THD 值,而帶有 400 V 電機的 800 V 逆變器由于在較小的調(diào)制指數(shù)附近運行而具有較高的 THD 值。
關(guān)于包括逆變器、APU 和車載充電機在內(nèi)的電力電子設(shè)備的可靠性,400-V BEV 和 800-V BEV 之間的主要區(qū)別在于從 650-V 開關(guān)更改為 1200-V 開關(guān)。一般而言,1200-V SiC MOSFET 已被證明非??煽浚⑶也粫霈F(xiàn) 3300-V MOSFET 中由于重復(fù)的三象限脈沖浪涌電流而導(dǎo)致的stacking faults。盡管很少有研究直接比較 650-V SiC MOSFET 與 1200-V SiC MOSFET 的可靠性。有文獻比較了 650-V/10-A 和 1200-V/19-A SiC MOSFET 之間的柵極-氧化物退化,通過閾值電壓、柵極-平臺電壓和柵極-平臺時間測量。它發(fā)現(xiàn),雖然這三個參數(shù)在所有器件的實驗測試期間都有所增加,但發(fā)現(xiàn) 650-V/70-A 器件的總體偏移要高得多。這是由于較高額定電流器件的柵極氧化層面積較大,這意味著柵極氧化層退化在具有較高額定電流的 SiC MOSFET 中更為明顯。由于 400-V BEV 需要更高額定電流的器件,所以 800-V BEV 中的 MOSFET 可靠性可能會略高于 400-V BEV 中的可靠性。第二個考慮因素是直流支撐電容器的壽命。根據(jù)汽車級金屬化聚丙烯薄膜電容器制造商 Vishay的說法,電容器壽命由工作電壓與額定電壓和溫度的比率決定。因此,如果工作溫度相似并且選擇具有相同額定值的電容器(即,600V 電容器用于 400V BEV,1200V 電容器用于 800V BEV),則電容器壽命應(yīng)大致相等。
總而言之,轉(zhuǎn)向 800-V 電池使設(shè)計選項可以使用標(biāo)準(zhǔn) 400-V 電機或 800-V 電機。保留 400 V 電機的主要優(yōu)點是在車輛重新設(shè)計時需要較少的工程量。然而,第 III 節(jié)已經(jīng)表明,由于 800 V 下電機的電磁性能得到改善,從電機的角度來看,800-V 電機有利于提高電機功率密度。從逆變器的角度來看,第四部分表明,在 800V 電池和 800V 電機之間使用的逆變器將具有更高的效率、更好的 THD、更低的直流支撐電容器尺寸和成本。此外,與標(biāo)準(zhǔn)的 400V 動力系統(tǒng)相比,全 800V 動力系統(tǒng)將具有更高的逆變器效率和類似或略高的可靠性。因此,電機和逆變器分析都顯示了向 800-V 動力系統(tǒng)發(fā)展的前景。
小結(jié)
本文總結(jié)了在電動汽車中采用 800V 電氣系統(tǒng)的好處和挑戰(zhàn),主要目的是提高快速充電率,這可能會促進電動汽車的應(yīng)用推廣。
----對于更高電壓的 800 V 電池,由于需要傳輸更少的電流,從電池傳輸電力的車載電纜將具有更小的尺寸和質(zhì)量。但是,為了監(jiān)控更多串聯(lián)電池,BMS 成本將增加,并且需要更高的電池組連接器、保險絲和電纜額定電壓。此外,更大的電氣絕緣可能導(dǎo)致更大的包裝。
---- 對于電機,由于在弱磁區(qū)增加電機功率,更高的直流母線電壓將導(dǎo)致更高的功率密度。然而,由于更高的機械應(yīng)力(來自更高的轉(zhuǎn)速)和防止 PD 的需要,電機設(shè)計變得更加復(fù)雜;本文討論了將 PD 考慮因素納入電機設(shè)計的一般方法。
---- 對于考慮了兩種逆變器情況:800-V 逆變器(在輸入端)為 400-V 或 800-V 電機供電。分析表明,逆變器與 800V 電機配對可產(chǎn)生最高的效率和最低的濾波電容器要求。
審核編輯:劉清
標(biāo)簽: